Control unit for open-loop sun tracking collectors
1.Overview
Sun tracking collectors are dynamic devices because they have to rotate around one or two axes, the so-called tracking axes, to follow the apparent daily movement of the sun.
Collector rotation around each axis requires a driving unit. The type of the drive unit assembly depends on the size and dimensions of the collector. Drive units composed of an electric motor and a gearbox combination are used for small collectors (aperture area less than 100 m2), whereas powerful hydraulic drive units are required to rotate large collectors.
Local control units currently available on the market can be grouped into two categories: (1) control units based on sun sensors (closed-looped tracking) and (2) control units based on astronomical algorithms (open-loop tracking). Control units in group 1 use elements such as photocells, tube shadow band and flux lines to detect the sun position, whereas those in group 2 calculate the sun vector using very accurate mathematical algorithms that find the sun elevation and azimuth every second and measure the angular positions of the rotation axes by means of electronic devices (angular encoders or potentiometers attached to the rotation axis).
In concentrating systems (such as parabolic trough, dish, Fresnel lens, etc.), the required level of tracking accuracy is typically in the order ±0.1o for each axis. In the case of open-loop control, the overall tracking error is combined from the calculation error, the mechanical drive errors (such as backlash, motor accuracy etc.) and the collector mechanical errors (such as a difference created between the angle measurement plane and the receiver plane). To reach the desired, overall accuracy of ±0.1o, the calculation accuracy should typically not exceed ±0.01o.
Closed-loop tracking can be accurate enough but by nature, is rather expensive due to the additional equipment and complexity. On the other hand, to reach a calculation accuracy of 0.01o with an open-loop control, one typically needs a PC or a micro-computer - devices which are definitely not robust enough for 20-30 years operation, expected for solar systems. In addition, computers do not always allow a high calculation speed which is critical for sun tracking. Thus, a simple, low-cost, accurate and robust control unit for sun tracking is not yet available in the market.
To deal with that challenge, CMC has developed a low-cost open-loop control unit based on coding the highly accurate but complex, NREL astronomical model (uncertainty < 0.01o - see below) on a compact, 32 bit Programmable Logic Controller (PLC). The robustness is obtained
by the nature of the PLC itself while the required accuracy is obtained by the NREL model implemented by the 32 bit resolution. In addition, the advanced programming language, sitting on the PLC, allows fast calculation, in the order of ms. The product was tested successfully in a two-axis tracking system of a spherical collector at the Technion Institute of Technology, Israel (see annex).
2. Sun Position (astronomical) Model
The NREL report [1] is a step by step procedure for implementing a Solar Position Algorithm (SPA) to calculate the solar zenith and azimuth angles in the period from the year -2,000 to 6,000, with uncertainties of ±0.0003o. The collector tracking angles can be always derived from the solar zenith and azimuth angles. For instance, in point focus systems (2-axis tracking), the collector azimuth angle could be the solar azimuth itself and the collector elevation angle could be the solar zenith complementary (90o-zenith).
To our best knowledge, to obtain an overall calculation uncertainty of less than ±0.01o, the hardware resolution should be at least 32 bit.
Another important feature of the SPA is the calculation of sunrise/sunset times which allows smooth and automatic operation of the entire solar plant.
3. The PLC
The PLC main specifications are listed in table 1 below. The controller is shown in Figure 1.
For more information, see the manufacturer manual file attached.
Table 1. Controller specifications
Parameter |
Value |
Manufacturer |
Jetter |
Model |
JC-340 |
Resolution |
32 bit |
Accuracy |
<±0.01° |
Speed |
133/166 MHz |
Calculation time |
2÷50 ms |
Programming language |
STX |
MTBF |
>20 years |
Tasks in parallel |
Up to 100 |
Customer programming interface |
Yes |
I/O number |
256 - |
Operating temperature |
0÷50°C |
1. CMC is the exclusive importer of Jetter controllers in Israel.
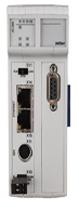
Figure 1. The JC-340 controller. The physical dimensions are 50 mm×100mm×131 mm.
Advantages
1. Durability and robustness. The PLC is much more reliable than a PC or a micro-computer, which a MTBF larger than 20 years.
2. Accuracy. The <±0.01o is obtained by the 32 bit resolution (see section 2).
3. Calculation speed. The STX programming on a 32 bit CPU allows fast calculation. The max calculation time is only 50 ms. For instance, a ladder diagram programming on a 24 bit controller could result in a calculation time of 30s which is way too high for sun tracking purposes.
In contrast to ladder diagrams, the STX language has architecture similar to C/C++. Thus, simple calculations do not store variables in memory - only functions do and there is no physical calling for functions. In addition, the STX allows a direct approach to memory variables.
4. Analog output. The controller can directly drive stepper motors which are a preferable choice in small collectors (Figure 2). Stepper motors are more accurate than dc motors due to the fact that they don't include encoders (or potentiometers). Due to the high Transmission rate and the additional electrical resolution increase, the tracking error created by the stepper motors units (see section 1) is negligible.
5. Programmability and flexibility. The controller can be programmed by the customer which allows high level of flexibility and independency for the customer.
For example: in parabolic trough collectors, due to the high moment of inertia, a tracking shift of about 0.05° can be created by the collector motion itself. However, in this controller, a PI or PID function (calculation) can be easily programmed to diminish that error.
The high I/O number allows integrating plenty of analogue sensors to the controller. The applications could be, for instance, performing temperature and flow control in the PLC.
6. Communication and deployment. The TCP/IP protocol allows each PLC to control up to 20 axes (or 10 collectors: 10×2 axes = 20) connected in series. The controllers are connected in parallel to a PC through a router. The network for large scale solar systems is presented in Figure 3.
The network features are:
- Number of connected controllers is unlimited.
- Distance is unlimited.
- Allows controllers' communication to a single PC where data can be stored, processed and presented.
- Each PLC has two Ethernet outputs when the PLC-router connection is only using one. The other output can be used for failure detection, etc. such that maintenance actions do not force disconnection of the controller from the network.
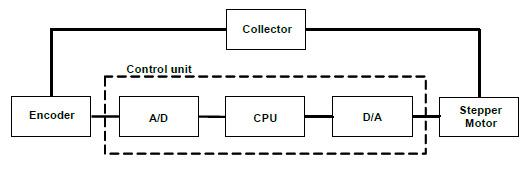
Figure 2. The control unit with a stepper motor drive system
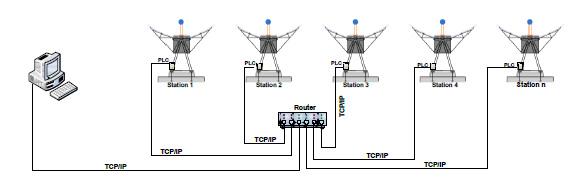
Figure 3. The PLC network and deployment – large scale solar systems. The controllers are connected in parallel to a PC through a router. In the PC, data can be stored, processed and presented
References
- . I. Reda, A. Andreas (2005) Solar position algorithm for solar radiation applications, NREL Technical Report, NREL/TP-560-34302.
Appendix – the project at the Technion (Haifa, Israel)

Figure 4. The collector at the Technion. The tracking is controlled by the CMC controller.
Download Article \ הורד מאמר
Confidentiality Warning:
The information contained in this document is confidential and subject to certain laws pertaining to the protection of proprietary information. It is intended only for the use of the individual or entity named above. If the reader of this message in not the intended recipient, or the authorized agent thereof, the reader is hereby notified that retention or any dissemination, distribution or copying of this transmission is strictly prohibited. If you have received this document in error, please notify us immediately by reply e-mail or by telephone, and delete all copies of the original message.
Thank you.